Cleaning procedures have become more and more important in the pharmaceutical manufacturing environments and they have been recognized as critical steps in the improvement of the final product quality.
IWT’s daily mission is to deliver the finest equipment in one of the highest regulated environment’s existing. Our absolute focus is to achieve regulatory compliance, to accomplish the validation of both systems and processes, to install quality in every engineering phases and to exceed any safety standards.
IWT cleaning systems are developed following worldwide standards and guidelines:
- ISO9001
- EU GMP (Annex 11 and 15 above all)
- FDA 21CFR part 11 for software and part 210-211 (GMP)
- ASME – BPE
- GAMP5
- ISPE Baseline
- Ph.Eur and USP
IWT products meet the EU requirements (CE marking) as well as UL/CSA standards.
The final goal of any validation is to assure the equipment under testing is not only suitable for the intended purposes but that it is also built according to the user’s requirement specifications - meeting, if not exceeding, guidelines and industry standards.
At IWT we strongly believe that communication with our clients is the key for a successful partnership. Several protocols and documents are shared upfront in order to set clear and definitive project targets, which will constitute the bases for designing and manufacturing phases as well as benchmarks for all the commissioning activities.
Our comprehensive documentation includes:
- QPP Quality project plan
- FDS – HDS – SDS normally provided and commonly agreed
- FAT, SAT IQ/OQ and OQ Alarms
- WPS-WPQR certifications
- RX analysis of the welding
- Calibration SOPs and certificates
- Materials and components traceability matrix
- Change control system whenever required
Once the on-site handover is accomplished, our team of highly skilled technicians will always be available to support any PQ and/or cleaning validation activities you might require as part of your specific quality insurance protocols.
The design of the washing equipment and relevant accessories has an enormous impact on time, efficiency and throughput of the cleaning processes. Proper engineering also influences how easily and ergonomically material can be circulated from production lines and washing areas or for CIP applications how quick and effective the in-place setup will be. In order to minimize the downtime between your production batches, IWT always applies a risk based approach in the evaluation of your needs, layouts and working procedures with the aim to release quality products with a perfect blend of performance, timing and cost.
Years of experience and multiple complex projects managed for multinational companies result in a solid knowledge and understanding of the cleaning dynamics. These are the cornerstones of IWT expertise to deliver different level of custom solutions to match your unique application to process: product contact parts, format parts, tanks, drums and bins, glassware, trays ...and many more! All units manufactured feature premium quality components selected from top brands and long term durability.
Mechanical design according to the industry standards and guidelines is then complemented by a user friendly control system that is GAMP5 and 21 CFR Part 11 compliant and by a PLC code based on a Siemens platform.
All the software is developed in house by our team of dedicated engineers to guarantee the full responsibility on analysis and validation of the code itself, this combined with a complete code handover to clients are meant to speed-up and simplify both maintenance and troubleshooting activities.
The human machine interface (HMI) provides a simple gateway for users to build the most suitable cleaning cycle according to the different loads.
Different user access levels (4 available as standard) grant full protection of the systems against unauthorized logins.
An embedded Ethernet connectivity allows integration of the washers with SCADA systems to manage (for example) electronic transfer of the batch reports, setting and troubleshooting from a remote location, as well as date and time synchronization with the company network.
All IWT systems are designed with safety in mind for both operator and process.
A full risk analysis and consequent HAZOP is part of the early engineering phases to provide equipment capable to deliver safe, repeatable and reliable cleaning results.
Calibrated probes, sensors and specific controls are embedded to guarantee a real time monitoring of critical parameters and accurate process diagnostics.
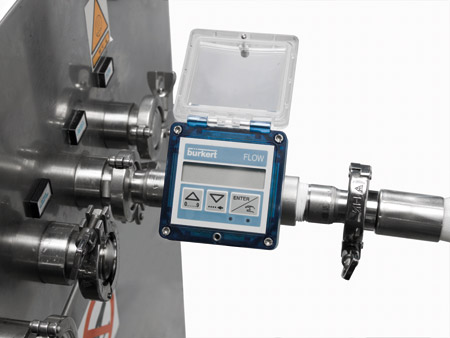
A safe process ensures not only a clean load exceeding the QA acceptance criteria but also prevents any possible cross contamination between product batches and any microbial growth during inoperative phases.
To do so all the washing machines are designed for full drainability and cleanability of chamber, pumps and piping.
The bio-seal separation and door interlocking system which allows the unload door to be open only when the cycle is duly accomplished, permits a perfect separation between loading and unloading areas when different levels of classification are necessary.